客户案例 | 化身炼钢厂“钢铁侠” D21助力告别高危人工巡检!
发布时间:2025年05月08日
炼钢厂作为现代工业体系的核心枢纽,犹如工业制造的"心脏",通过精准调控的高温冶金工艺,将生铁中的碳、硫等杂质去除并添加合金元素,生产出满足建筑、汽车、机械、能源等领域需求的结构钢、特种钢等数百种钢材产品。
某炼钢厂是华南地区重要的大型钢铁生产基地,其高炉区生产环境充斥着多重危险因素:高温热浪(钢水温度达1600℃以上,作业区环境温度常超50℃)、弥漫的金属粉尘(PM2.5浓度可达数百μg/m³)、刺耳的机械噪音(持续90分贝以上)、潜在的煤气泄漏(CO浓度可能瞬间超标),以及钢水喷溅、设备机械伤害等突发风险。恶劣的环境不仅严重威胁作业人员健康(易引发中暑、尘肺、听力损伤等职业病),更对传统人工巡检的准确性和安全性构成严峻挑战,任何细微的疏忽都可能引发重大安全事故。
为此,千巡科技通过在生产区部署 D21巡检机器人及AXS安巡系统,对生产区每个高炉的30根吹风管(近200个巡检点位)进行数据采集与预测分析,极大地提高了设备健康状态可视化程度,帮助客户实现从被动检修到预测性维护的转变,为高炉安全运行提供了可靠保障。
|| 安全隐患大
高炉区存在高温、高压、有毒气体、粉尘、噪音等危险因素,人工巡检需近距离接触这些区域。若出现疲劳、注意力不集中或经验不足还可能导致漏检或误判,易引发烫伤、中毒、爆炸等事故。
|| 效率低下
人工巡检受限于时间和体力,难以全面覆盖所有关键设备与巡检点位,且使用测温枪,每次仅能获取单个点位的温度数据;依赖纸质记录或手动输入,数据易丢失、篡改,难以及时同步到管理系统,影响故障响应速度。
|| 成本高昂
需配备大量专职巡检人员,并定期培训安全规程、设备知识等,长期人力投入较大。此外,突发事故导致的停产损失、人员伤亡赔偿等风险较高。
|| 主观性强
不同巡检员的技术水平、责任心差异可能导致检查结果不一致;人工观察难以精准测量温度、振动、气体浓度等参数,易遗漏潜在发展的故障。
|| 实时性差
人工巡检通常按固定时段排班作业,两次巡检间隔可能导致错过突发故障。待发现问题后需逐级上报,容易延误抢修时机。
|| 管理难度大
难以确保巡检员按规范操作(如是否到位、是否认真检查),即使使用打卡系统,也可能存在“代签”或敷衍了事。纸质记录不便存储和分析,难以通过历史数据预测设备寿命或故障规律。
钢铁厂智能巡检解决方案是针对传统人工巡检模式在高危高温环境下存在的安全隐患、作业困难、效率低下等问题而设计的系统性创新方案。该方案通过部署 D21巡检机器人及AXS安巡系统,构建了"端-边-云"协同的智能化巡检体系,实现了高炉区域全流程、多维度的无人化安全监测。
在硬件层面,D21智能巡检机器人搭载耐高温防护层,集成高精度双光云台,蜂鸣器、爆闪灯、气体传感器,能够完全替代人工进入高温区域,对高炉炉体、热风管道等关键部位实时采集可见光与红外热辐射数据,进行毫米级精度的全方位检测,大幅提高巡检效率。同时,其基于多传感器融合的智能避障系统可实时感知复杂环境变化,结合自适应路径规划算法,即使在定位异常情况下也能实现自主恢复,能够有效降低机器维护频次与设备运维成本。
在软件层面,AXS 安巡系统作为智能巡检体系的核心中枢,通过多维度功能模块实现数据价值最大化与运维管理智能化。系统不仅能实时监控机器人任务执行过程,动态展示其移动轨迹、工作状态,还支持在线灵活配置巡检任务,实现任务的快速下发与调度;同时,对机器人采集的温度、气体数据进行实时分析,借助可视化图表可直观呈现变化趋势,方便工作人员快速掌握高炉区的运行状态。此外,当检测到温度异常升高、有害气体浓度超标等危险情况时,系统会立即通过声光报警、短信、邮件等多渠道告警。
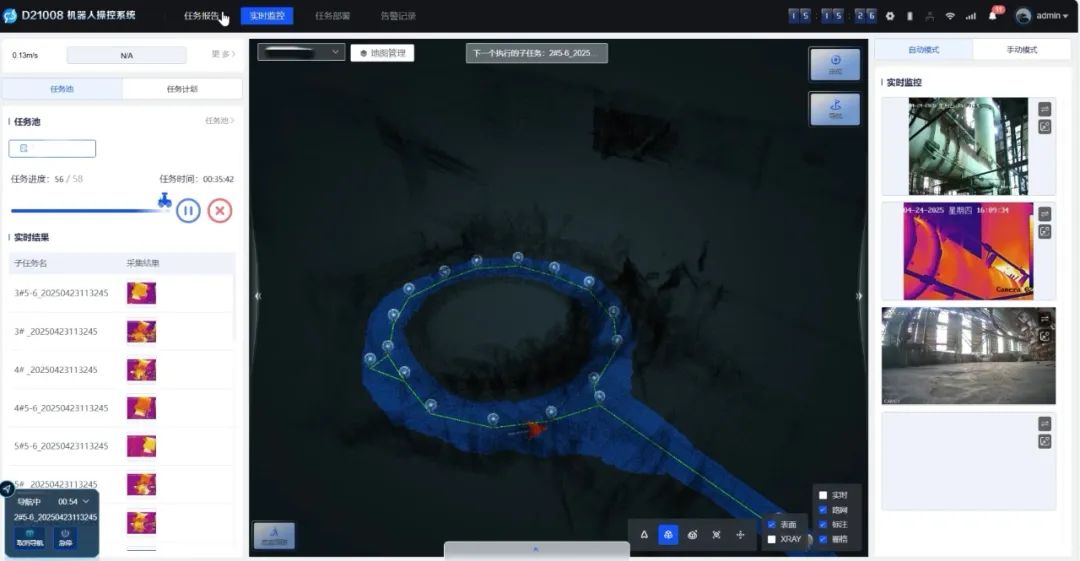
为进一步深化数据价值,系统运用机器学习算法对历史数据进行深度挖掘,建立设备运行健康模型,提前预测设备故障,实现预防性维护,从根源降低因设备突发问题导致的作业困难与安全隐患。在设备管理上,AXS 安巡系统构建完整的设备档案库,记录设备全生命周期信息,结合实时运行数据评估设备状态,科学制定维护计划。此外,该系统具备良好的开放性与兼容性,可与钢铁厂生产管理、能源管理、安全监控等系统无缝对接,实现数据共享与协同工作,例如根据生产计划自动调整巡检任务,联动安全监控系统进行全方位安全管控,达成高炉区域全流程、多维度的无人化安全监测目标 。
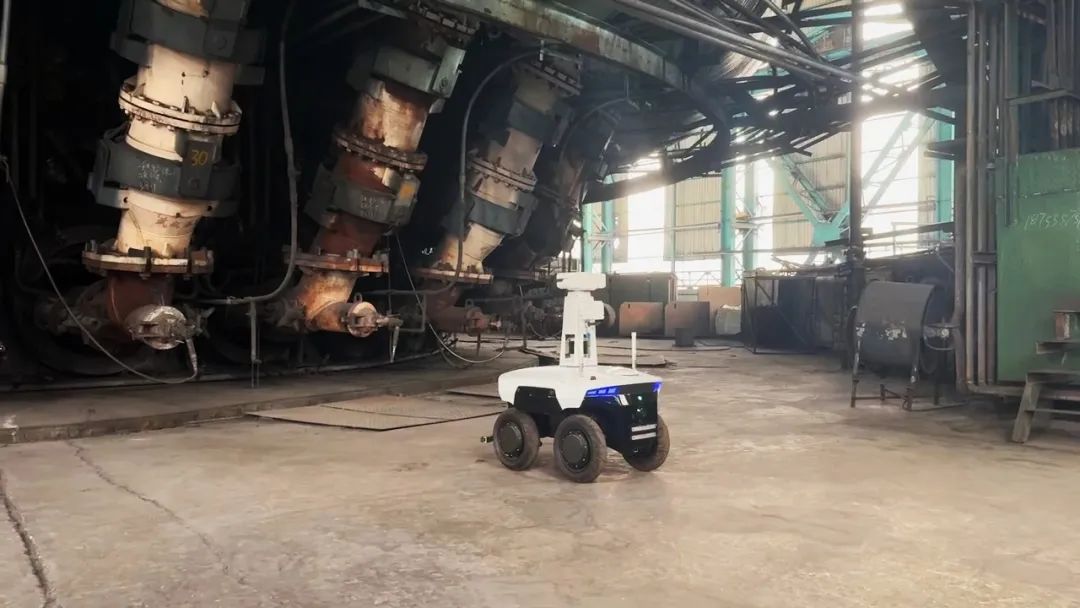

上一篇: 客户案例 | 多形态终端交付全站巡检运维
下一篇: 客户案例 | 多形态终端交付全站巡检运维